Coal-fired power plants
Cost Reduction and Downtime Prevention
Transport and storage systems at coal-fired power plants are exposed to significant volumes of bulk materials. Without adequate protection, frequent breakdowns and the need for repair or complete replacement of equipment can occur. Weartech provides a comprehensive range of products for wear protection, including ceramic, metal, and polymer products. Additionally, Weartech has extensive experience in providing friction reduction solutions, which is critical to preventing material flow delays in hoppers and silos. Weartech designs specialized solutions tailored to unique operating conditions, using a variety of materials from plastics to metals and ceramics, and our specialists are always ready to provide the necessary technical support.
Benefits of lining materials:
- Ceramic wear protection:
- Excellent protection against abrasive wear
- Lining available in the form of tiles, cylindrical elements, or seamless structures
- Thermal resistance up to 1000°C
- Metal wear protection:
- Effective protection under sliding and impact loads
- Thin-walled and self-supporting constructions
- High resistance to temperature fluctuations
- Combination of various materials:
- Maximum wear protection under various operating conditions
- Cost-effective protective solutions
- Weight reduction for optimized design
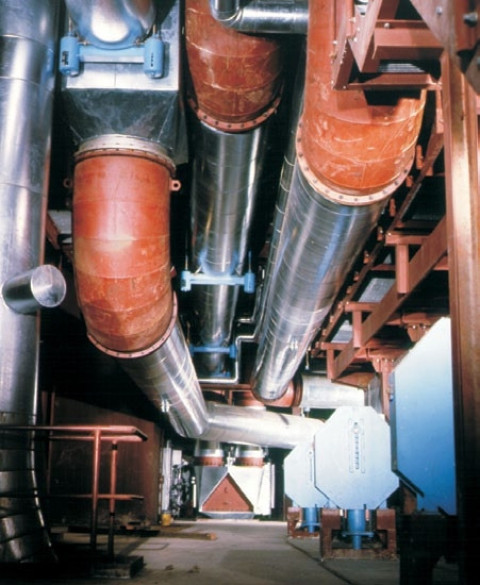
Approximate use of ABRESIST material for lining pipes that transport crushed coal in power plants
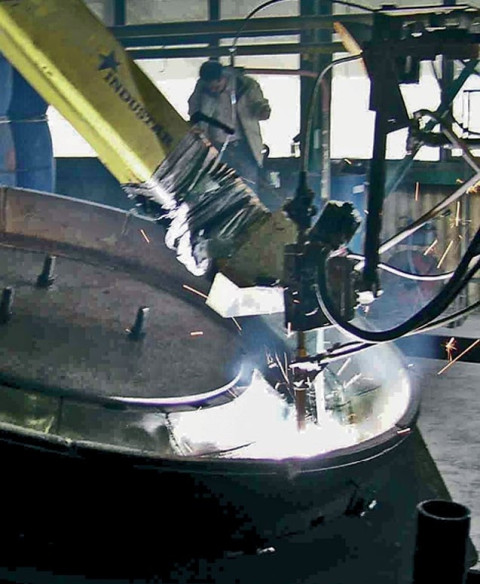
Refurbishing the coal grinding table using Weartech’s ULTRAPLATE material
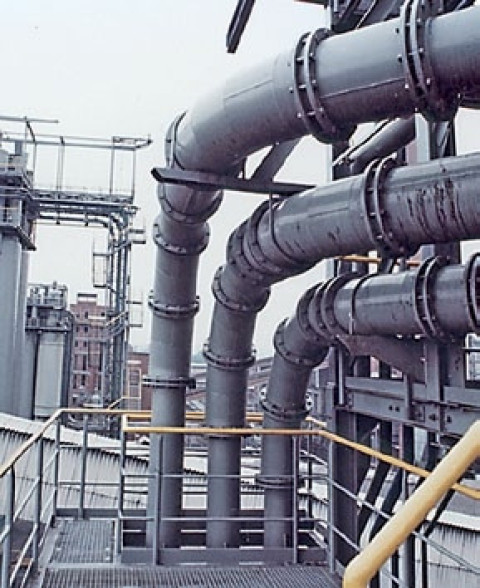
Ash removal pipes at power plants experience severe wear. Weartech provides durable materials, including ABRESIST, KALCOR, and KALOCER, to extend the life of these systems
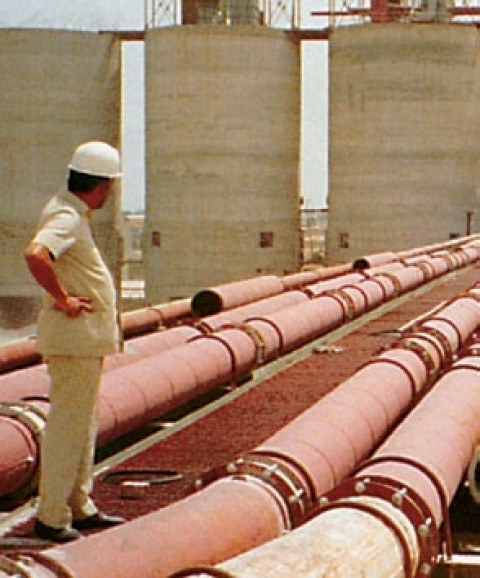
ABRESIST cast basalt is recognized as a standard in many countries for lining wet ash removal systems. The image illustrates its use at a power plant in India
Pipeline and Structural Node Upgrade Services
All elements of power plant infrastructure are subject to wear, which is especially important for components handling coal, such as crushing equipment, coal dust feed systems, and equipment for collecting and removing dust and ash. Desulfurization processes, including the processing of limestone and gypsum, also require wear protection.
Materials used for long-lasting performance include:
- ABRESIST - Durable cast basalt
- KALCOR and KALCOR-S - Zirconia corundum and its sintered analog
- KALOCER - Aluminum oxide-based ceramics
- KALCRET - High-strength compound
- KALSICA - Durable silicon carbide-based ceramic material
- KALMETALL-C - Strong and reliable cast iron
- ULTRAPLATE - Wear-resistant hardfacing
These materials can be combined to optimize technical and economic performance under coal-fired power plant operating conditions.
Coal Loading, Unloading, Grinding, and Feeding into the Burner
Protective material for separators in coal crushing systems, proven over years of use - cast basalt ABRESIST, is used worldwide.
To ensure the reliability of separators, hardfacing ULTRAPLATE and high-strength compound KALCRET are often used, forming a smooth, seamless surface.
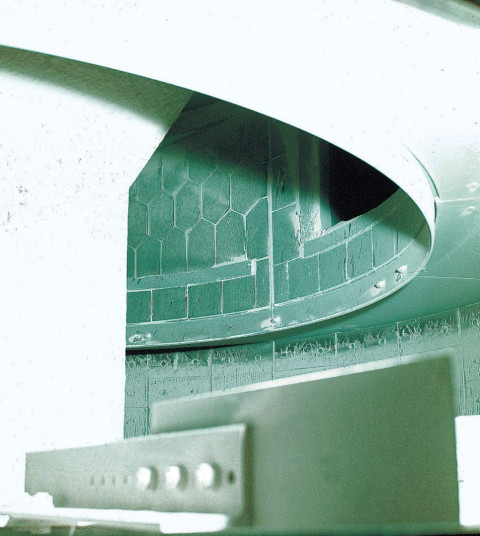
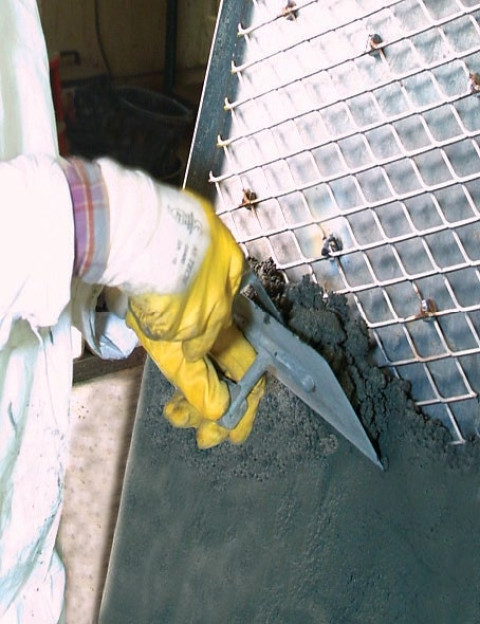
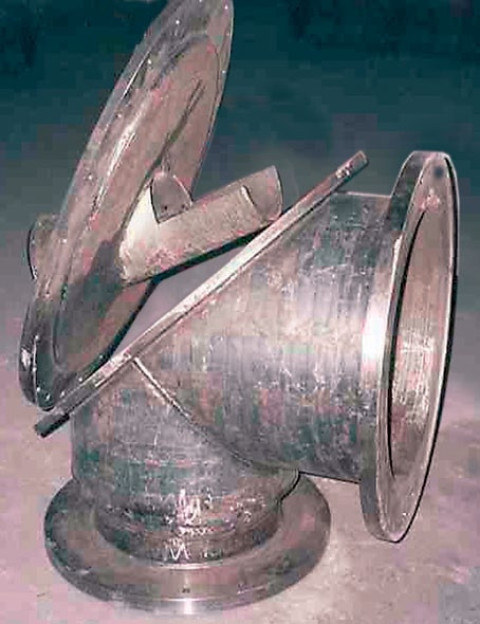
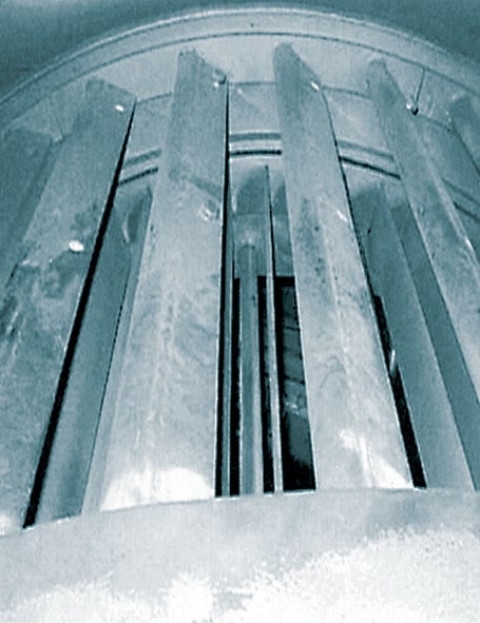
Reliable Wear Solutions
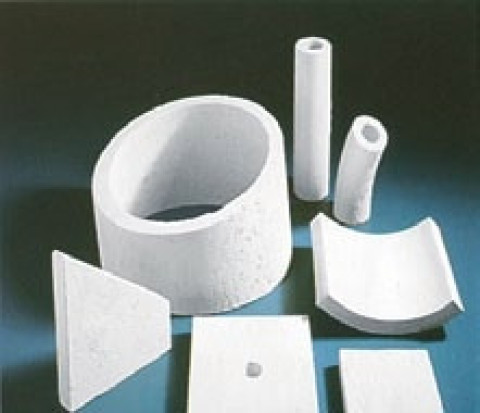
KALOCER: Durable alumina ceramics for power plants, resistant to wear and corrosion
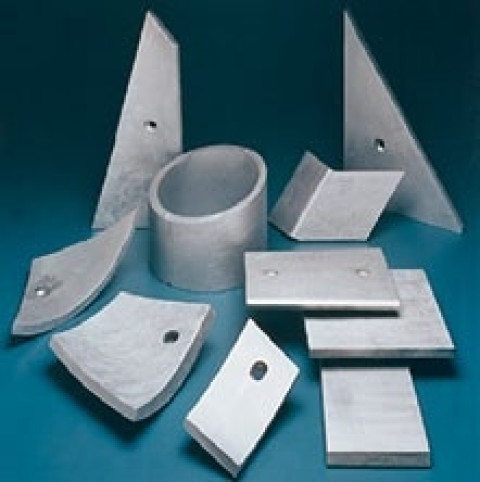
KALMETALL-C: Durable cast iron, optimized for high resistance to abrasion and impact
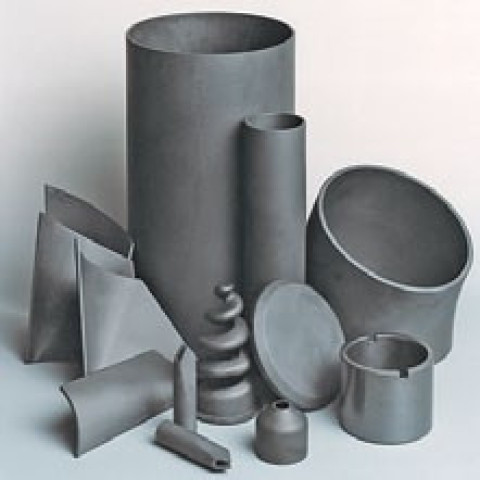
KALSICA: Wear and heat-resistant silicon carbide ceramic material for equipment protection
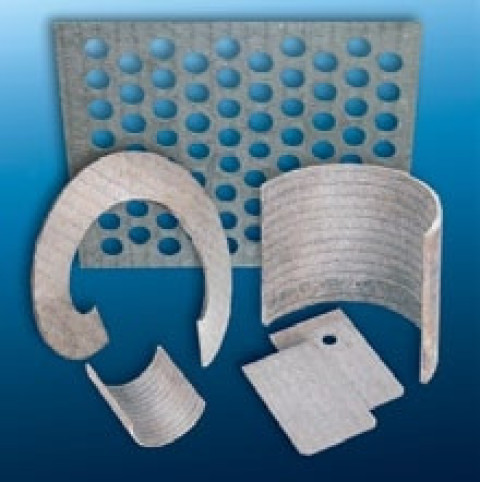
ULTRAPLATE: Chromium carbide hardfacing, wear and impact-resistant, self-supporting
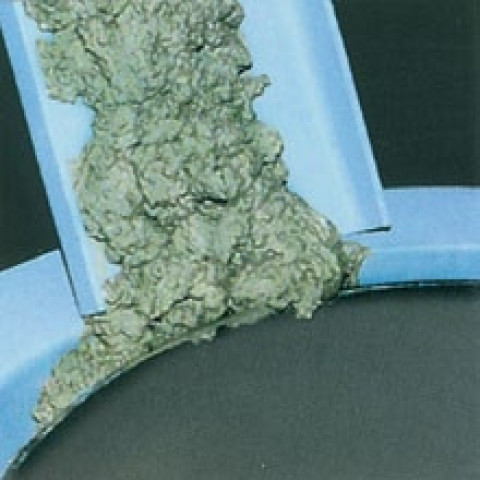
KALCRET: Durable compound for seamless coating with excellent wear, pressure, and heat resistance
Solutions for Pulverized Coal Transport Systems
Diverse combinations of protective coatings for pipelines with diameters ranging from 400 to 800 mm are successfully applied in real conditions. By varying materials according to operational parameters, such as particle sizes, ash content, and throughput volumes, equipment lifespan can be increased to ten years or more.
- KALCRET: Versatile compound for creating seamless protection with non-standard cross-sections.
- Combination of KALCOR and ABRESIST: Multiple materials combined to create cost-effective protection.
- KALMETALL-C for coal dust pipes: Durable coating enhancing wear resistance.
- Zirconia corundum KALCOR: Effective in combination with transition elements for pipes up to 488 mm in diameter.
- KALCOR-S: Used for large segments attached to thin walls for uniform strength.
- Wear-resistant cast iron KALMETALL-C: Extends pipeline lifespan, effective in limited-budget upgrade scenarios, as shown on 700 kg and 518 mm diameter pipe elbows.
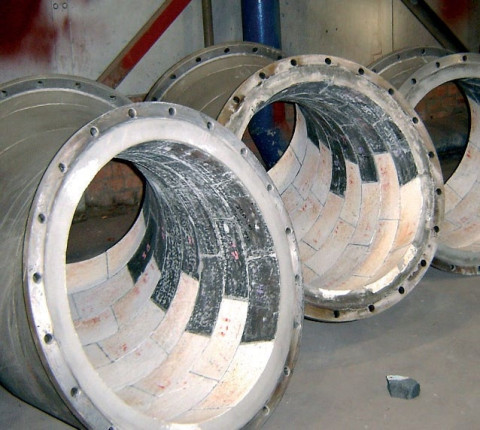
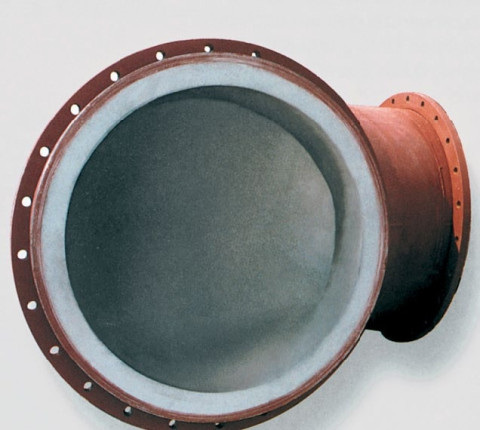
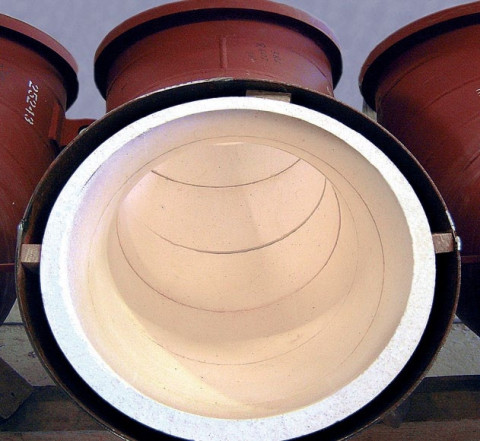
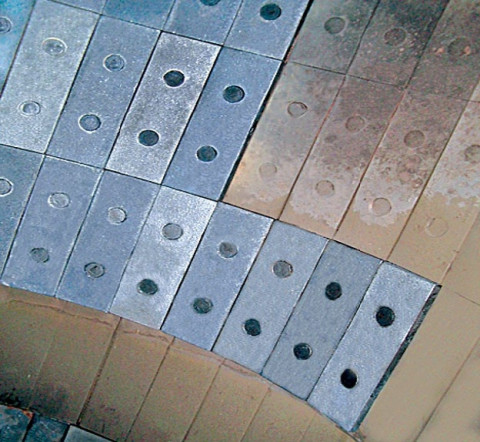
The following technologies are also applied:
- ULTRAPLATE: Creates reliable structures for coal dust pipes, reinforced with additional protective layers.
- KALOCER: Enhances the strength of coal dust pipes through thin-layer solutions using ceramic material.
- KALCOR: Distribution blocks provide additional surface wear protection.
- KALCOR-S: Ceramic distribution blocks resistant to intensive use.
- ULTRAPLATE for shaft protection: Material ensuring the protection of rotating components from wear.
Ash Removal and Flue Gas Desulfurization
To ensure the efficient operation of ash removal and flue gas processing systems at coal-fired power plants, the following technologies are used:
- KALICA: Protective ceramic coatings enhance equipment resistance to abrasion during dust transfer.
- KALCRET and ULTRAPLATE: High-strength compounds for protection against high-temperature gases and abrasive wear.
- KALCOR and KALOCER: Materials for protecting pipes and channels from mechanical and corrosive damage.
- ABRESIST: Wear-resistant material for high-wear areas, reducing repair frequency.
Experience in Wet Ash Pipeline Protection
For many years, Weartech has been supplying wetted ash transport pipes internationally, usually providing them with ABRESIST cast basalt protective layers. This material is among the proven choices and serves as reliable protection in this application field.
ABRESIST combines high wear resistance and excellent corrosion protection. The lifetime of pipeline systems is typically over 20 years. Practically, no material in this price category has such a long service life.
Weartech supplies wet ash transport pipes in various configurations, with internal diameters ranging from 200 to 500 mm. Steel casings can also be effectively protected from corrosion.
Pipe connections are usually made using flanges. However, any connection option is possible. Additionally, welded or screwed connections have also proven effective in practice.
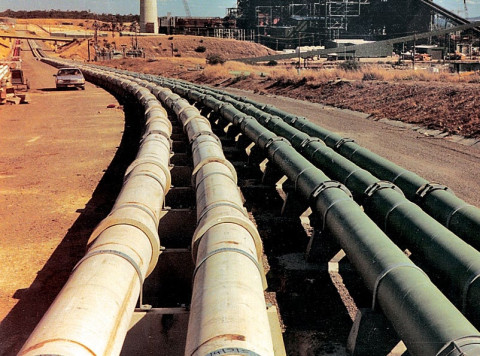
Using Victaulic couplings for pipes in Australia
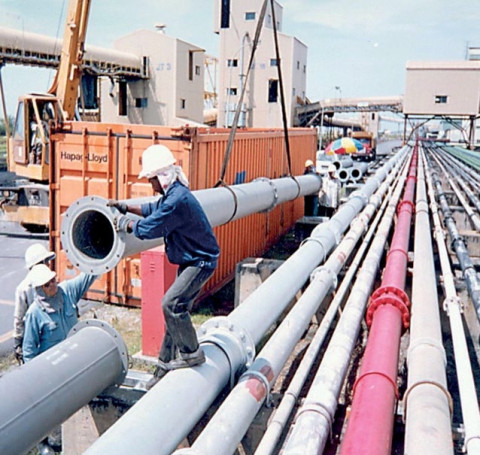
Installation of a wet ash removal pipe system in Malaysia with a diameter of 350 mm
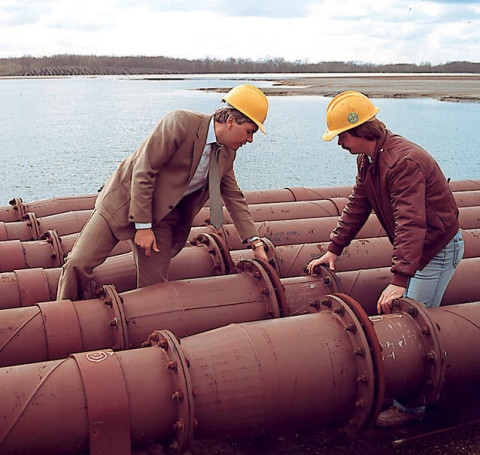
Use of compensators for joining sections of long pipelines
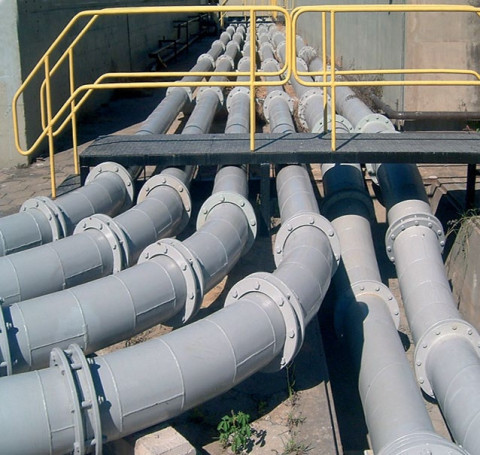
Pipeline networks from different complexes converging at a centralized waste processing point in Brazil